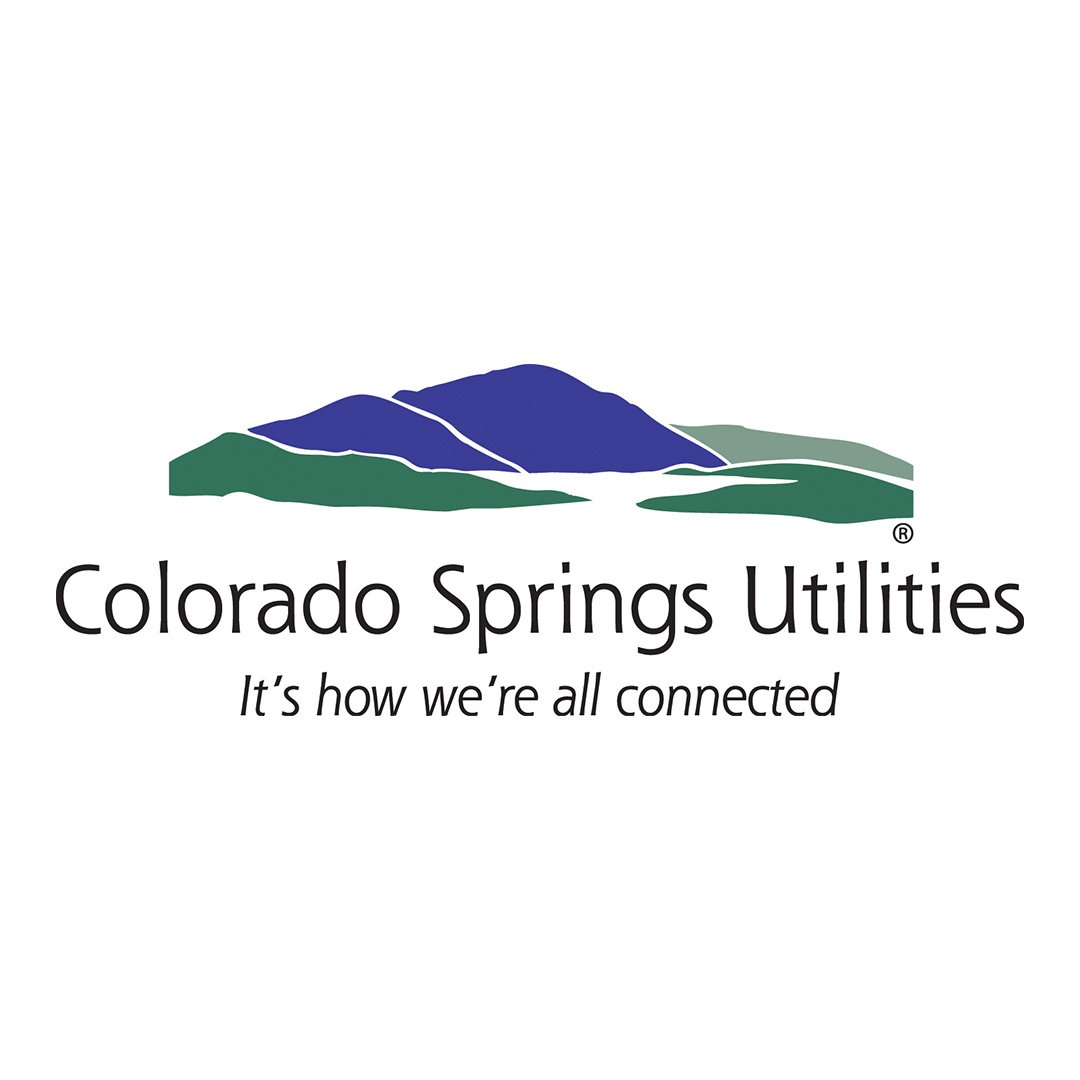
Steve B.
Duration: 1 minute
Published on November 9, 2023
The average power plant has thousands of moving parts and electrical connections, from very large to very small. While the way we generate power will dramatically change in the future, local electric generation at large power plants is still important. Considering the criticality of our local power plants, our plant managers strategically target maintenance periods for when demands are at the lowest – such as early fall or late spring.
“When and how we conduct planned maintenance on a power plant seems straightforward, but there’s so much more to it and it’s not a universal approach across the industry,” says Ian Gavin, power plant manager. “It’s a process that is dependent on a lot of unique variables – fuel source, local climate, age of equipment, etc. However, since the COVID pandemic, we’ve had to be even more strategic in our approach, to include navigating supply chain delays and parts availability.”
In late September, employees at both the Front Range and Ray Nixon Power Plants – located just south of Colorado Springs – began planned maintenance and inspections on various components inside the facilities. The challenge, as always, is to have all work completed in a tight window to be ready for colder weather and higher demands.
“Thankfully, we planned far enough in advance to accommodate potential parts delays and other challenges, so we were ready to hit the ground running in late September,” said Gavin.
At the natural gas-fueled Front Range Power Plant, employees have been tackling a wide-range of maintenance and inspection tasks. This includes transformer work, motor control center replacements, oil changes on components and large gasket replacements.
“Maintenance on a power plant is on a whole different level when compared to that of other general industry,” said James Towell, plant superintendent, outage management. “Many of the parts are huge, from gaskets the size of a manhole cover and blades you’d see on a helicopter to motors the size of a small vehicle. Considering the size and scope of this equipment, it’s critical that employees are in continuous communication to ensure everything is de-energized and safe to work on.”
While the Front Range Power Plant was taken completely offline, staff performed a dual task at the coal-fired Nixon Power Plant – perform maintenance and repairs at one generating unit, while keeping the other units online.
“Implementing a strategic maintenance program while also meeting customer needs is definitely not a new challenge for us,” said Gavin. “I’m proud of our legacy to keep our power plants running for 100 or even 200 days straight, especially when they’re needed the most. This not only maintains reliability, but also manages costs for our customers. It’s something that doesn’t happen by accident and is in large part thanks to our plant employees and the dedication they have to their craft.”