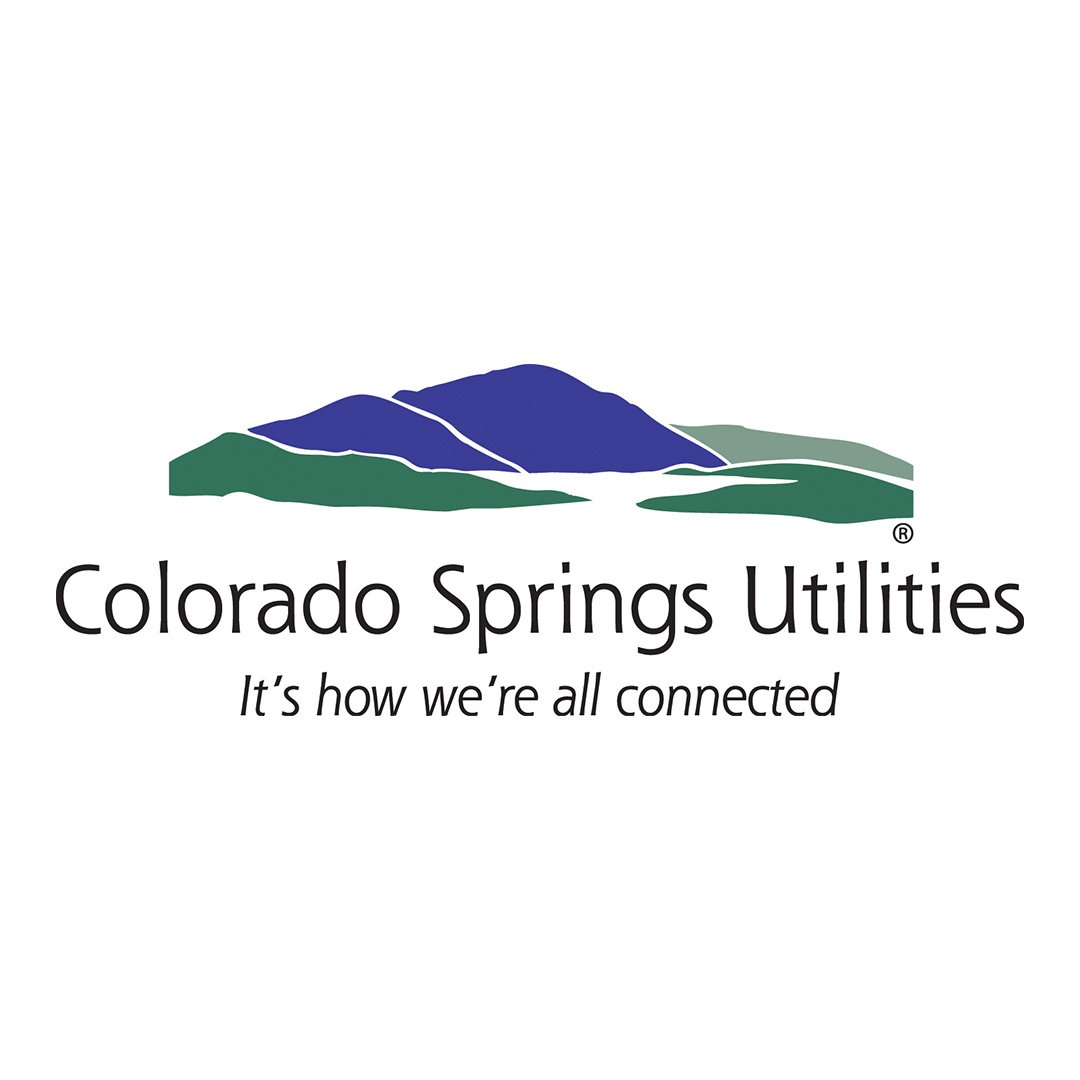
Steve B.
Duration: 1 minute
Published on October 13, 2022
Since the pandemic, the phrase, “supply chain” has become household vernacular and is no longer confined to the people who order products and raw materials on behalf of their organizations. From grocery supplies and auto parts to appliances and new cars, we’ve all been impacted by supply chain challenges.
Utilities around the United States – including Colorado Springs Utilities – continue to feel supply chain repercussions as well.
There are a lot of moving parts – both figuratively and literally – to keep a large and complex four-service utility like ours operating reliably and safely each day. Beyond fuel costs, the need to acquire new equipment and maintain existing pipes and wires with new parts can be a significant driver of the rates you pay.
The list of raw materials and equipment enlisted to keep a four-service utility functional and safe is extensive. There are rare earth metals and specialized steel required for certain equipment, along with clamps, wires, pipes, poles, turbines, electrical panels, filters, valves, meters, large electric switches and transformers.
According to a July 2022 article titled, “Transformative Times” in T&D World magazine, the utilities-related supply chain challenge is perfectly encapsulated by the many obstacles utilities around the nation are facing to acquire electric transformers.
To highlight the importance of electric transformers, the T&D World article and the Energy Department’s Office of Electricity points out that 90% of the electricity consumed in the United States passes through a large power transformer.
To put the critical nature of transformers into local context, Springs Utilities has about 40,000 transformers on our system, with about 400-500 needing replacement each year.
Transformers do not come in a “one-size-fits-all” model. Instead, transformers must be designed to unique specifications of each electric system. What may work on our electric grid, would likely not work on a grid in Ohio.
Additionally, transformers require expensive and often rare materials like copper and specifically milled steel. They are also designed by specially trained engineers and assembled by experienced technicians.
Despite the fact we’re well past the height of the COVID pandemic, the flow of transformers and the materials required to build them remains delayed and costs are inflated. With few domestic manufacturers and a reliance on imports, the problem is only exacerbated.
Before the pandemic, a transformer could be acquired within a year. Now, it’s about 38 months instead of 38 weeks for large, substation transformers; and 60 weeks (vs. 12 weeks pre-pandemic) for smaller single- and three-phase transformers.
Two teams at Springs Utilities tasked with managing these supply chain challenges – from pipes and wires to transformers and switches– are our in-house Apparatus Shop and Supply Chain Management teams.
Prior to the pandemic, supervisor David Buckner and his small team in the Apparatus Shop had the foresight to request additional help to increase their focus on more in-house refurbishments rather than always purchasing new equipment.
In 2020 alone, the team saved more than $640,000 by rebuilding and repairing existing equipment rather than purchasing new. Now, with the supply chain challenges of the last 2-3 years, those savings have grown to more than $1 million annually by having in-house expertise to squeeze more life out of aging equipment.
“I’m no Nostradamus, but in hindsight, it feels good to know we were ahead of the pandemic curve,” says Buckner. “It’s not just the monetary savings that are important, but also the reassurance that we’re doing everything possible to maintain system reliability and manage costs with the resources we have.”
Buckner emphasized that considering the size and scope of our electric system, purchasing new equipment will remain a necessity, especially as the electric grid evolves and technology changes.
Tasked with managing this challenge is Supply Chain General Manager Rich Norton.
“The pandemic-triggered supply chain problem is slowly improving, but we still have a tall task ahead,” says Norton. “To offset some of these challenges, we’re increasing our min/max inventory levels; expanding to international sources of supply; and collaborating with supply chain working groups from around the nation to locate equipment and confirm availability.